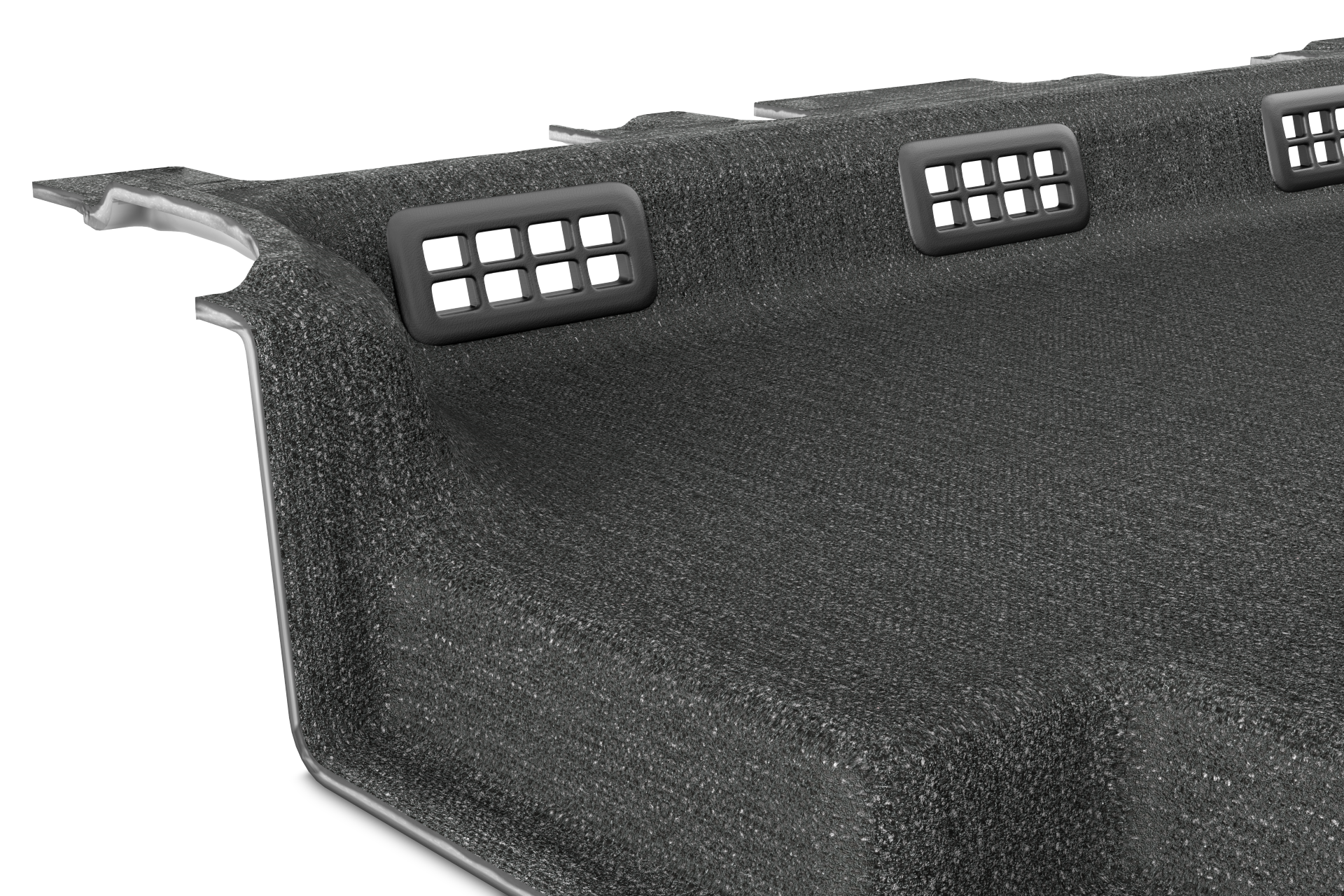
突破性的新型连接方案--大众ID Buzz项目地毯出风口格栅的紧固连接
Adler Pelzer公司以高品质和可靠的汽车内饰解决方案而知名,该成功案例展示了Adler Pelzer公司如何采用MultiMaterial-Welding公司的技术方案,在大众ID Buzz项目上采用创新的变革性功能零部件和地毯的连接方式,从而提升连接性能并降低总的成本。
Industry:
Automotive
Client location:
Germany
The Journey to Innovation
After years of collaboration with Bossard and familiarity with the MultiMaterial-Welding technology, Adler Pelzer reached a pivotal moment in early 2023. A phone call from Adler Pelzer stated: “We have a project where we need MultiMaterial-Welding.” Adler Pelzer was commissioned to produce carpets for the Volkswagen ID Buzz. Ventilation holes were mandatory, and the initial approach involved directly cutting holes in the carpet, which left room for technical and aesthetic improvements.
Addressing the Initial Challenge
The project’s objective was to find a reliable solution for securing the ventilation grid in the carpet, which posed unique challenges due to its soft and flexible nature. The initial approach used a two-piece clipping solution for the ventilation grid. However, this method proved inadequate because the carpet’s softness allowed it to bend in any direction, causing the clips to fail. This inadequacy highlighted the need for a more advanced and dependable solution. LiteWWeight® Lotus functionally integrated parts (FIP) is exactly the right solution in this case. It can be integrated into the injection molded part, which simplifies production, reduces costs and enables complete design freedom.
The Solution: Testing MM-Welding®
Adler Pelzer recalled the MultiMaterial-Welding solution they had previously encountered. They were immediately convinced by the solution; however, more tests were needed. First, to test the welding on a wet carpet, since the carpet will be waterjet trimmed prior to MM-Welding process. Secondly, to test with SLS (printed) prototypes in full carpet which will be built in an actual car for the OEM for evaluation. The testing was organized quickly, and the solution proved to be more sophisticated and reliable. The integration of LiteWWeight® Lotus geometry with the plastic ventilation grid allowed the part to be welded by an ultrasonic machine within seconds from one side only in the carpet.
Innovative Technology
The innovative technology involves the partial liquefication of Lotus’ teeth into the fibrous material, creating an unbeatably strong connection with the textile structure. This solution not only shortened the cycle time drastically due to one-sided installation and fewer parts involved, but it also allowed for design and form freedom, improving overall aesthetics. Additionally, there was a 50 % reduction in parts needed, leading to cost and weight savings.
Successful Prototyping and Production
Thanks to the versatility of the product and the engineers’ skill in design and prototyping, the LiteWWeight® Lotus solution proved ideal for this project’s challenges. Initially, the application was intended for the production of 6 and 7-seater variants only. However, after the first prototypes, the OEM was convinced by the better visual appearance and aesthetics that it was also decided for the running series production of the 5-seater variant, resulting in the increase of the volume by 40 %.
Customer Benefits
- Revolutionary solution: This advanced approach tackled the challenge of securing ventilation grids in soft, flexible carpet material, providing a reliable and efficient alternative to previous methods and allowing design and form freedom.
- State-of-the-art technology: This cutting-edge method involved the partial liquefaction of Lotus’ teeth into the fibrous material within seconds, drastically reducing cycle time and improving reliability.
- Optimized production: With one-sided installation and fewer parts involved, cycle time, overall weight, and costs are significantly reduced.
- Elevated aesthetics: The nature of the functionally integrated parts and the possibility of one-sided installation significantly enhance the overall aesthetics.
A New Benchmark
Adler Pelzer’s innovative approach with MultiMaterial-Welding solution has significantly improved the reliability and efficiency of automotive interior parts. This success story with the Volkswagen ID Buzz project highlights the importance of continuous innovation and customer-centric solutions in the automotive industry. Together with Bossard, they developed a new benchmark solution for the carpet assembly in automobiles. The success is a joint effort of the openness and confidence from Adler Pelzer and the technical excellence of MultiMaterial-Welding technology, which justifies the solution.
Products used in this project
Hear it from the customer

"We’ve known about MM-Welding technology for a while, yet we were positively impressed by the problem-solving mindset of the team, creating value to the solution by using fully its outstanding performance in the product. It not only addressed our technical issues but also added aesthetic value and boosted overall efficiency: in short, a very successful collaboration."
Elmedina Andelija Key Account Manager
Adler Pelzer Group