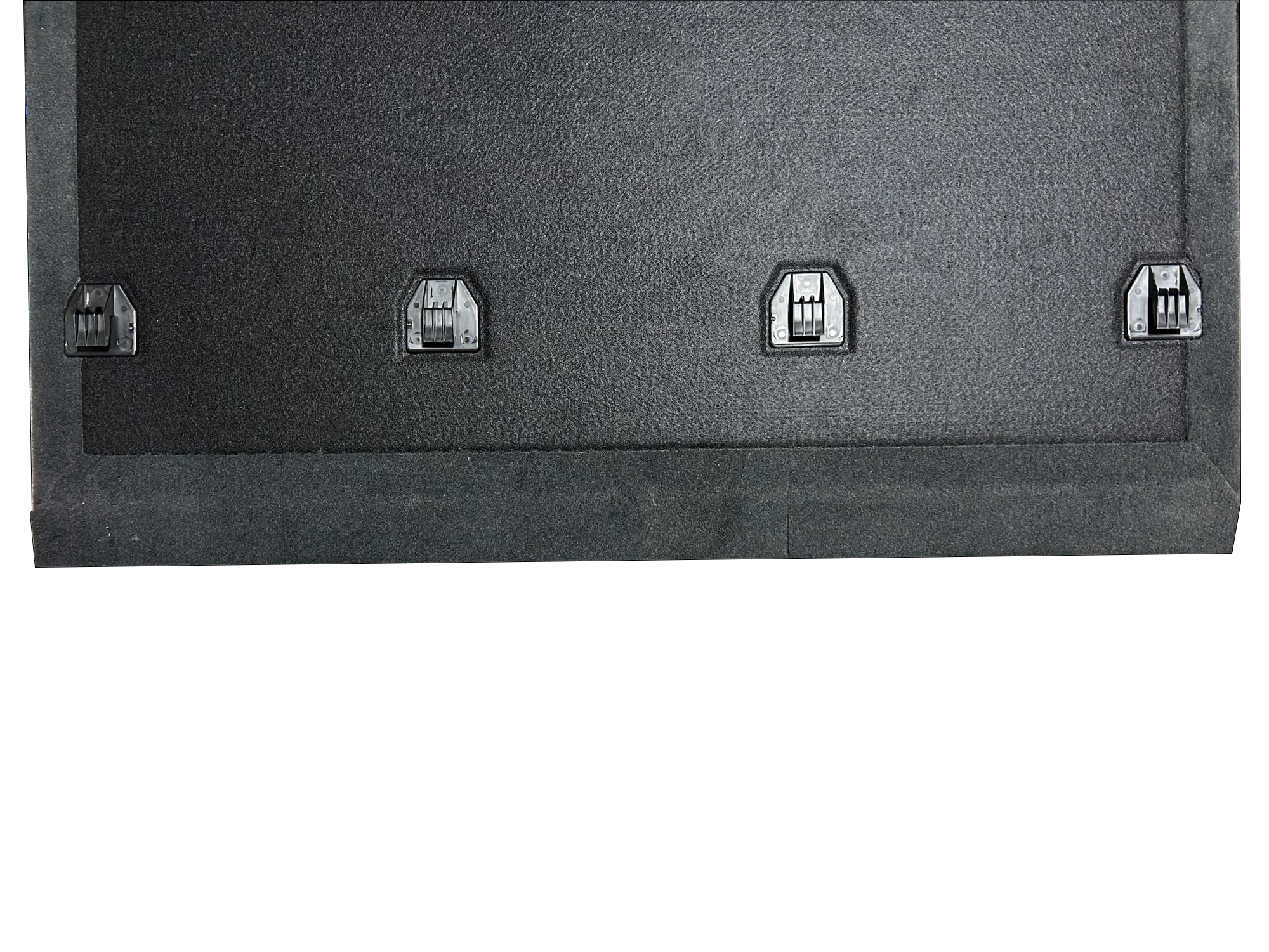
Simplified Assembly Through Innovative Load Floor Connection
Valley Enterprises successfully transitioned from manually attaching brackets using screws and t-nuts to an automated ultrasonic welding process. From overcoming the challenge of transitioning to ultrasonic welding, to reducing assembly components from 38 to 6 pieces, this is a story of technological success. Witness how close collaboration, open communication, and innovative thinking led to production efficiency reaching new heights.
Industry:
Automotive
Client location:
USA
Where it Begins
For three years, MM-Welding (MMW) cultivated a relationship with Valley Enterprises through consistent communication and exploratory projects. This collaboration reached a milestone when MMW demonstrated its capabilities in a load floor project for the Jeep Wrangler. This successful performance paved the way for a subsequent project with Stellantis’ Daytona/Charger. With the OEM already familiar with and confident in MMW’s solution, the project received swift approval.
The Challenge
Valley Enterprises faced a significant challenge: transitioning from manually attaching brackets with screws and t-nuts to a machine-based ultrasonic welding process. This shift demanded trust in the new technology and required a substantial capital investment in ultrasonic welding machines. To address these concerns, the MMW engineering team conducted multiple sample trials and prototypes, demonstrating superior performance compared to the existing method. The performance of MM-Welding technology met the OEM specifications and convinced Valley Enterprises of its efficacy. Moreover, the investment in the new machines was justified by comparable costs to current machines and labor expenses.
From 38 to 6 Pieces in Assembly
Traditionally, connecting the bracket in the load floor required 3 t-nuts and 3 screws. With MultiMaterial-Welding’s innovative LiteWWeight Pin, the pins and the bracket are now fully integrated into a single piece. This integration reduces each bracket’s components from 7 or 5 to only one piece, eliminating 32 parts in total during the assembly process. This significant reduction not only shortens cycle time but also lowers material and labor costs.
The Collaboration
Introducing a new connection method posed both technical and economic challenges, especially since the technology was unfamiliar to the customer. Despite the initial impression made by MMW’s solution, several sample trials and machine adjustments were necessary. However, this trial phase was completed smoothly and successfully. “The customer and the OEM were both very impressed and satisfied with the solution,” said Rob Tate, Business Development Manager. “They have always been very happy with the attention and communication from MMW and the Bossard team.” Close collaboration and open communication with the OEM were crucial to ensure MMW’s technology met all required specifications and could be trusted to deliver as promised.
The Solution
The LiteWWeight PIN geometry was licensed to Valley Enterprises for injection molding with the bracket together as one piece. MultiMaterial-Welding supported with machine design and sourcing to meet the requirements.
The LiteWWeight PIN Functional Integration addressed Valley Enterprises’ concerns on multiple fronts:
- Reduced parts on bill of materials: Simplified the assembly process by eliminating 32 parts on the lb load floor.
- Lighter weight solution: Enhanced vehicle efficiency and performance.
- Faster cycle time: Greatly reduced cycle time, improving production speed and efficiency.
- Cost savings on components: Lowered overall manufacturing costs.
The serial production is started in June 2024 with 140,000 vehicles per year and amounting to 2,24 million pieces of LiteWWeight PIN per year.
Production Efficiency at a New Height
Through innovative thinking and steadfast collaboration, MMW’s solution not only met but exceeded Valley Enterprises’ expectations. The transition to ultrasonic welding and LiteWWeight PIN technology streamlined their production process, resulting in a more efficient and cost-effective solution for the Stellantis Daytona/Charger load floors.