Discover the LiteWWeight® Pin from MultiMaterial-Welding AG, a revolutionary solution for effortlessly securing sandwich structures. This advanced fastener employs ultrasonic technology to ensure robust integration without the need for pre-drilling, redefining efficiency in assembly processes.
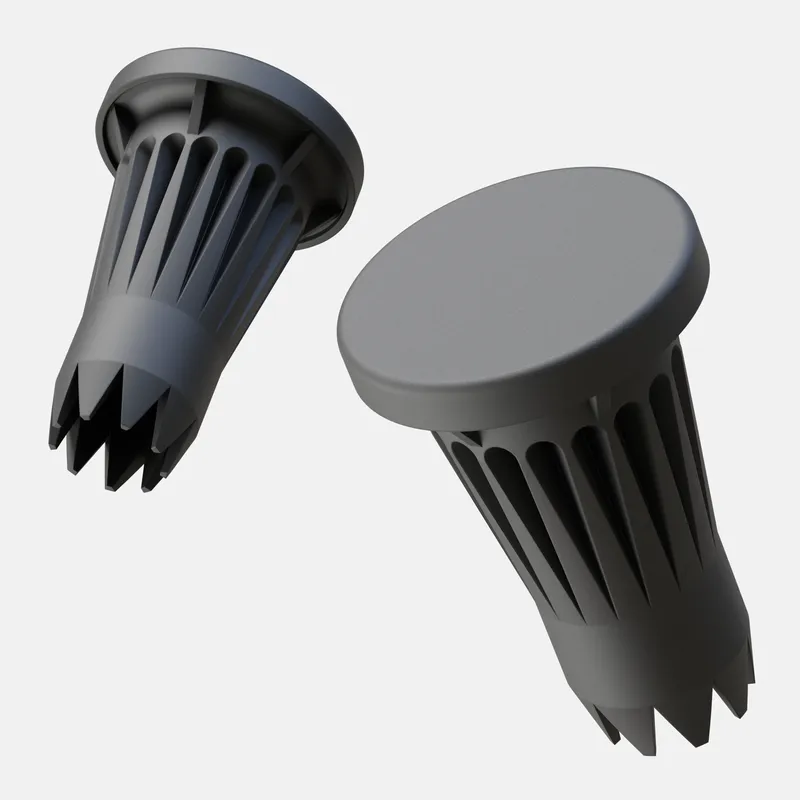
Variants:
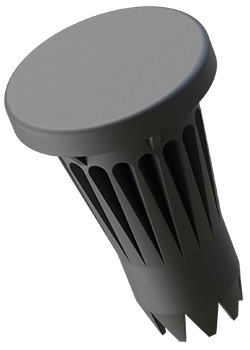
Standard
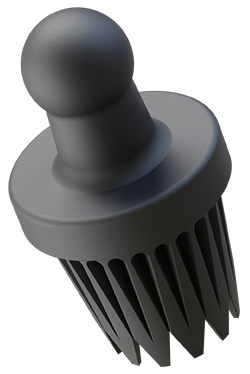
Ball-head
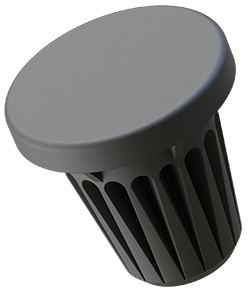
Sniper
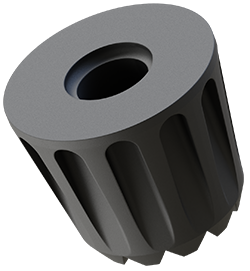
Adapter
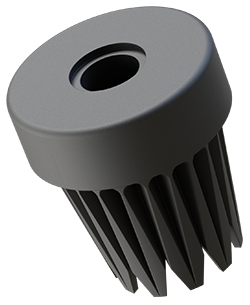
Universal
Substrate materials:
.png)
Sandwich panel (Baypreg)
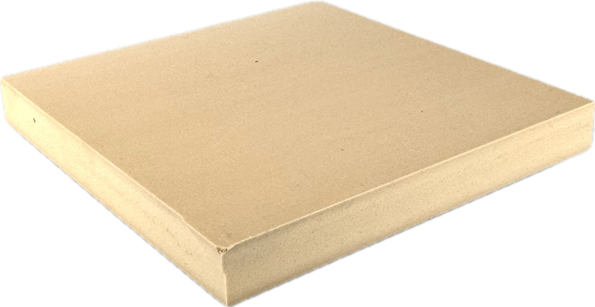
PU foam
Functionally integrated parts (FIP)
LiteWWeight® Pin connection geometry can be integrated into the injection molded part, which simplifies production, reduces costs and enables complete design freedom.
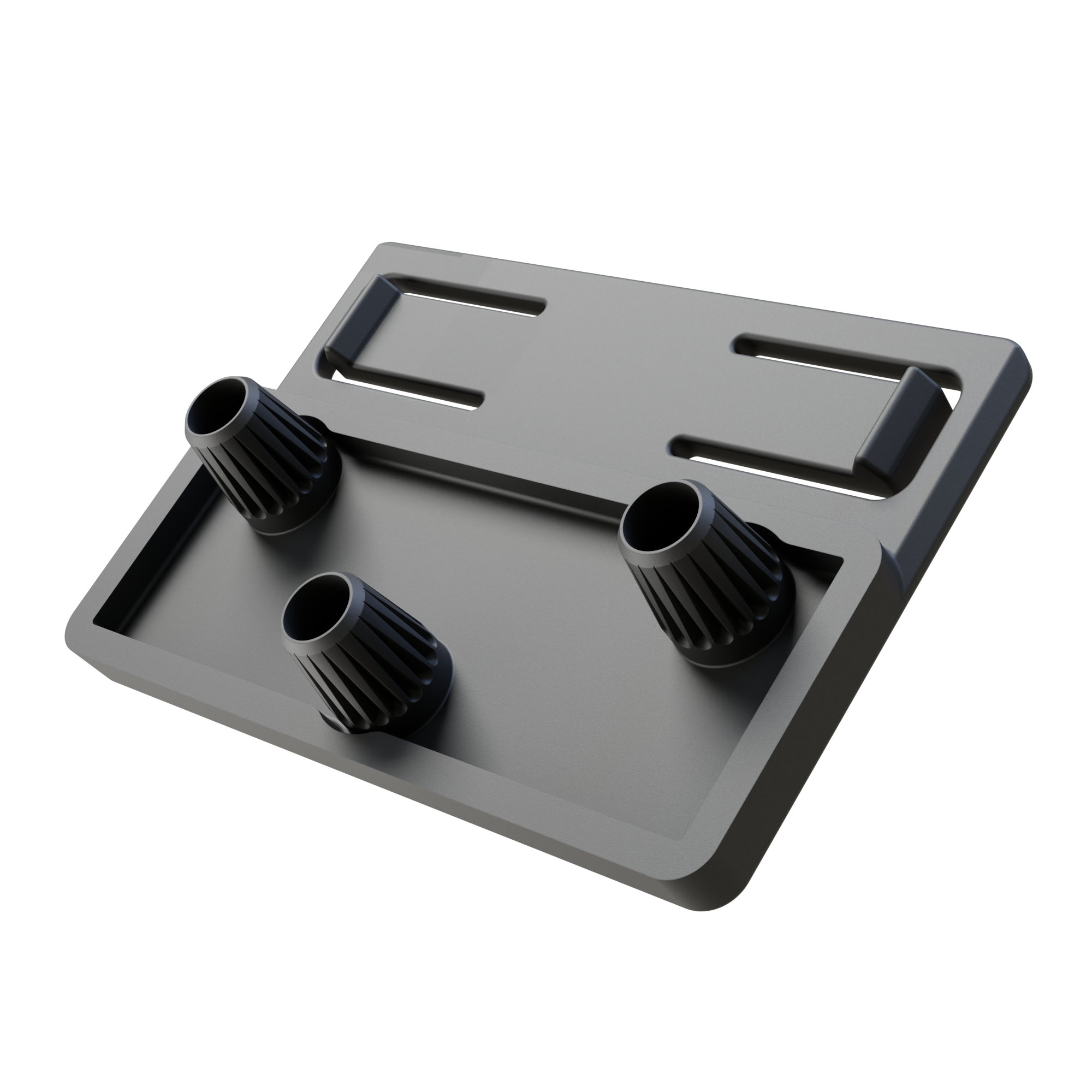
Advantages of FIP:
- Reduced cycle time
- Reduced costs due to the fast process and less parts to manipulate
- Higher Strength: With less material, higher strength can be achieved
- Easy one-sided access only assembly process # Geometric Simplification
- Connection geometry can be integrated into the part to connect
- Form freedom: No rotational symmetry required
- Improved aesthetics: No fasteners are visible
Our LiteWWeight® Pin is a revolutionary fastening solution, meticulously designed for honeycomb and sandwich panel applications. This fastener is a game-changer in the world of composite material assembly, offering unmatched efficiency and strength.
Key Features:
- Seamless Honeycomb Integration: Expertly crafted for honeycomb structures, ensuring high-strength bonding and compatibility with honeycomb panels and meshes.
- Rapid, Drill-Free Installation: Designed for quick installation in about 1 second, eliminating the need for pre-drilling in most scenarios, thereby streamlining the assembly process.
- Versatile Design: Suitable for diverse applications, including hidden fasteners for composite decking and edge placements in sandwich panels.
- Lightweight Yet Robust: Offers the perfect balance between reducing weight and maintaining structural integrity, ideal for lightweight composite materials.
- Eco-Friendly Manufacturing: Aligns with sustainable practices, reducing environmental impact through minimized waste and energy use.
Automotive application
Our technology is applicable to a wide variety of assembly parts.
Click on the parts to find out more.
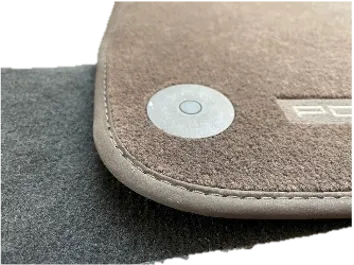
Floor mat
Robust fastening systems ensure floor mats remain securely in place, enhancing vehicle interior stability and safety.
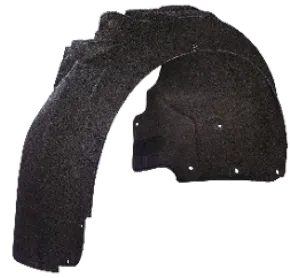
Wheel arch liner
Reliable fastening methods secure wheel arch liners, ensuring durability and protection against road debris.
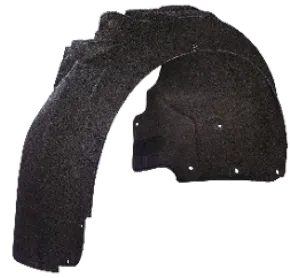
Wheel arch liner
Reliable fastening methods secure wheel arch liners, ensuring durability and protection against road debris.
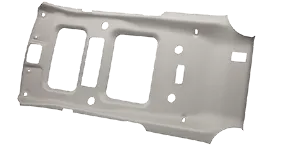
Headliner
Reliable fastening techniques ensure the headliner remains firmly in place, contributing to the vehicle's overall interior elegance and safety.
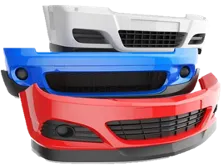
Bumper
Efficient fastening solutions ensure secure and durable attachment of exterior trim parts.
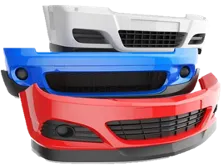
Bumper
Efficient fastening solutions ensure secure and durable attachment of exterior trim parts.
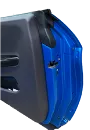
Exterior trim
Efficient fastening solutions ensure secure and durable attachment of exterior trim parts.
Load floor/trunk floor
Sturdy fastening solutions provide a robust foundation for load floors and trunk floors, ensuring durability and reliability in cargo management.
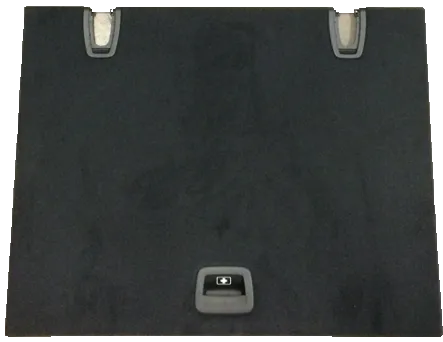
Spoiler
Reliable fastening solutions ensure a quick, secure and flawless assembly of spoilers.
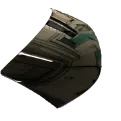
Spoiler
Reliable fastening solutions ensure a quick, secure and flawless assembly of spoilers.
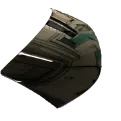
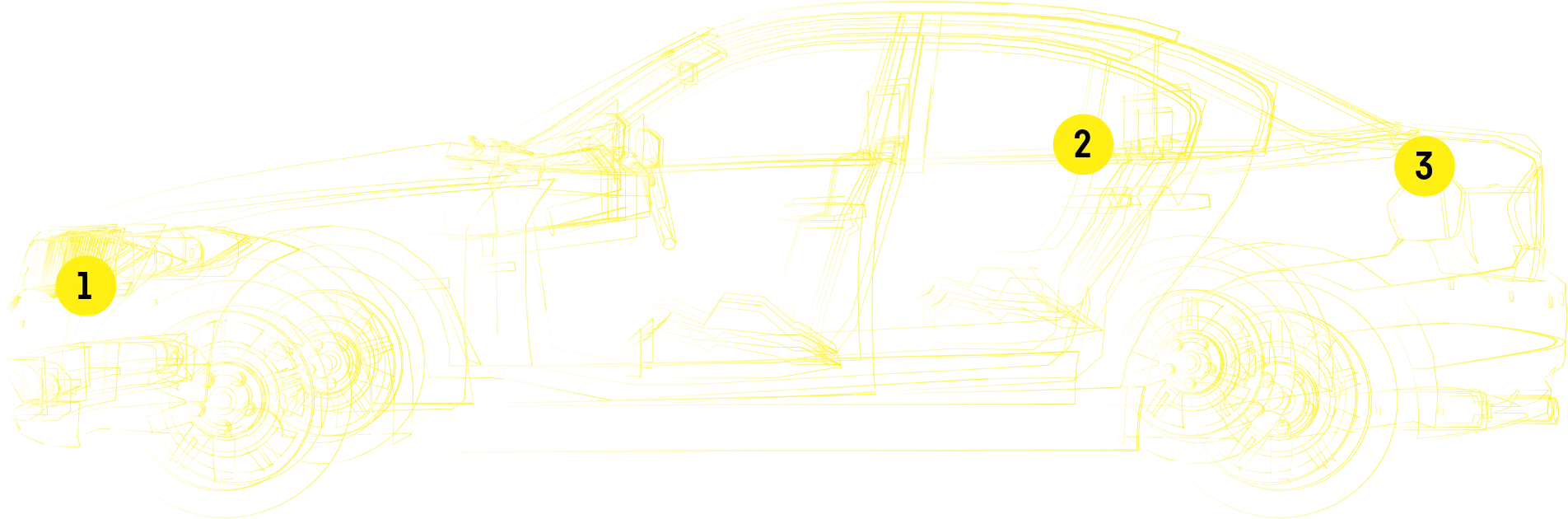
1. Bumper
2. Crash pads and protections
3. Trunk compartment
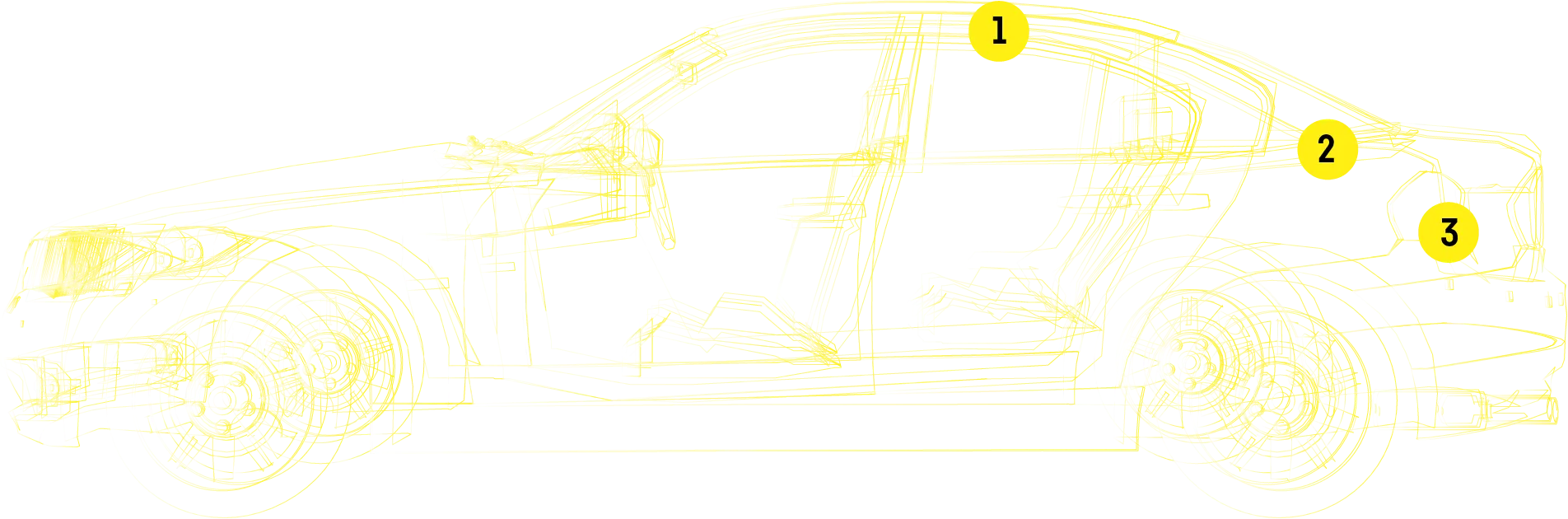
1. Roof panels
2. Parcel shelf
3. Load floor / trunk floor
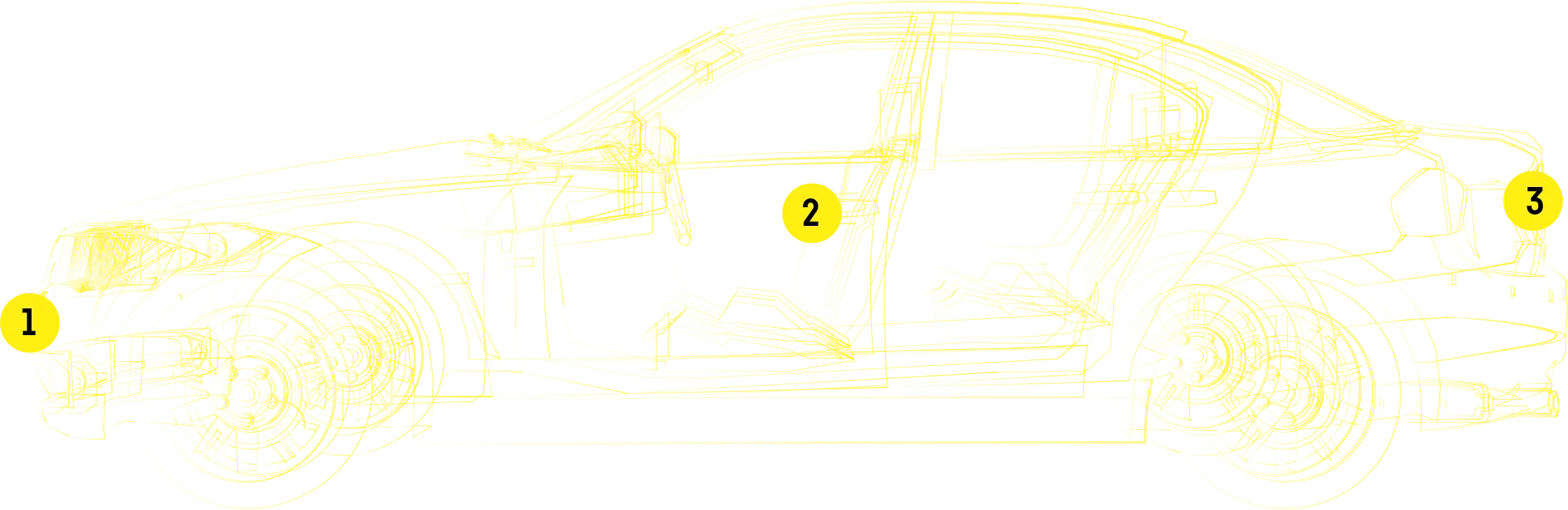
1. Bumper
2. Exterior trim
3. Spoiler
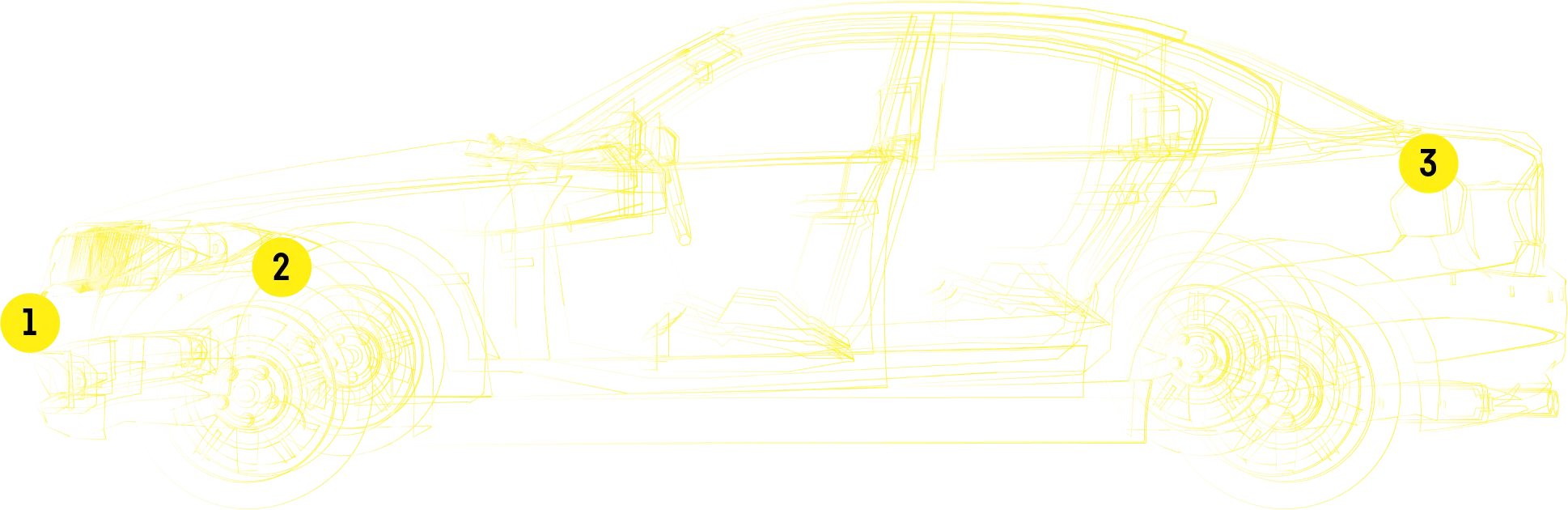
1. Exterior trim parts
2. Wheel arch liner
3. Spoiler
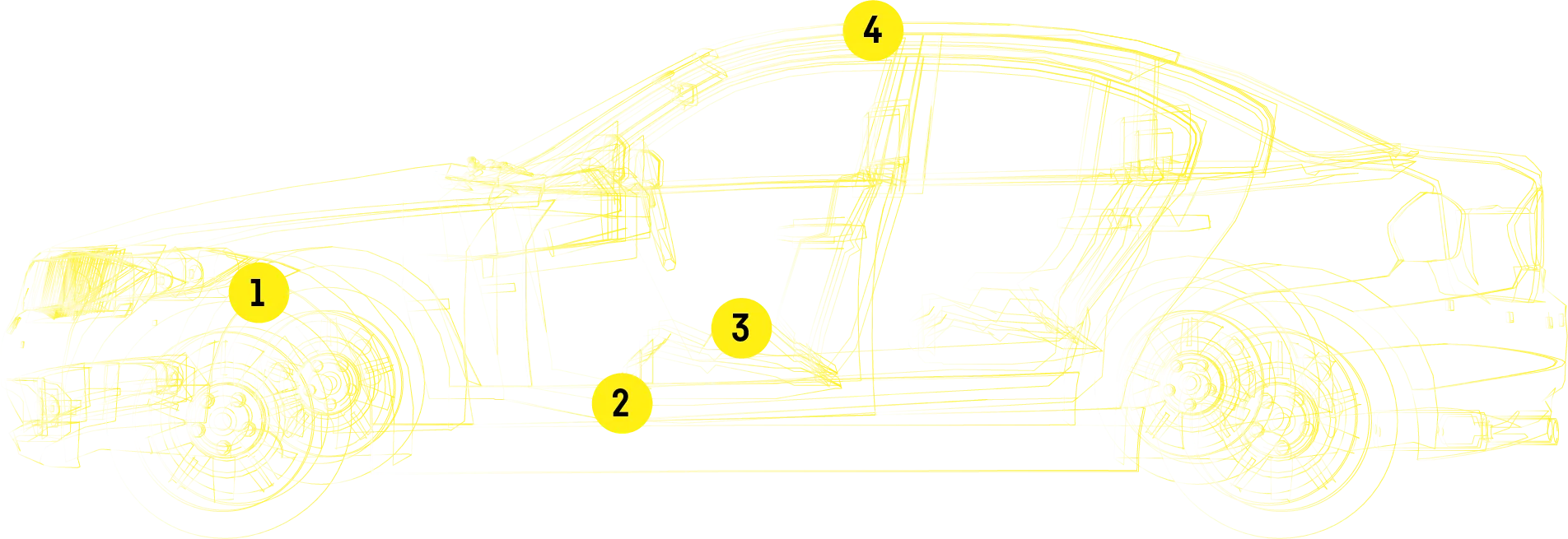
1. Wheel arch liner
2. Floor mat
3. Carpet floors
4. Headliner
Aerospace application
Our technology is applicable to a wide variety of assembly parts.
Click on the parts to find out more.
Plastic window covers
Robust fastening systems ensure plastic window covers are securely attached, enhancing safety and clarity in aerospace environments.
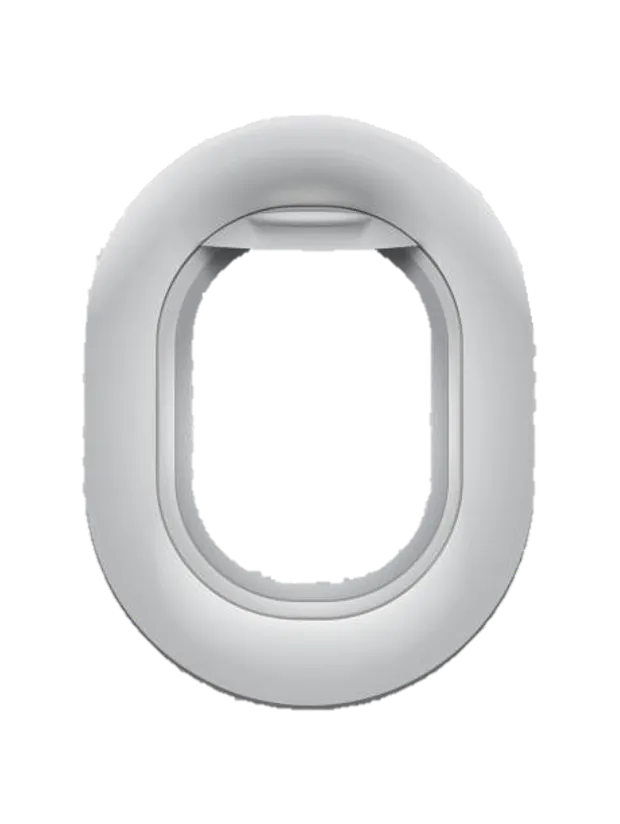
Galleys / kitchen
Secure fastening solutions maintain the integrity and functionality of galleys and kitchen areas in aerospace applications.
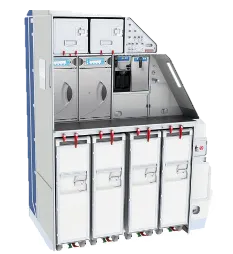
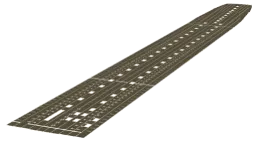
Interior floor panels
Durable fastening techniques ensure interior floor panels remain firmly anchored, contributing to cabin stability and passenger comfort in aerospace applications.
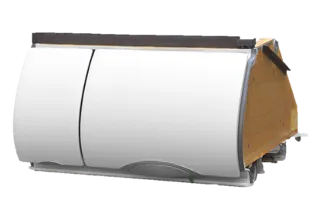
Overhead compartments
Efficient fastening solutions keep overhead compartments securely in place, ensuring passenger convenience and safety.
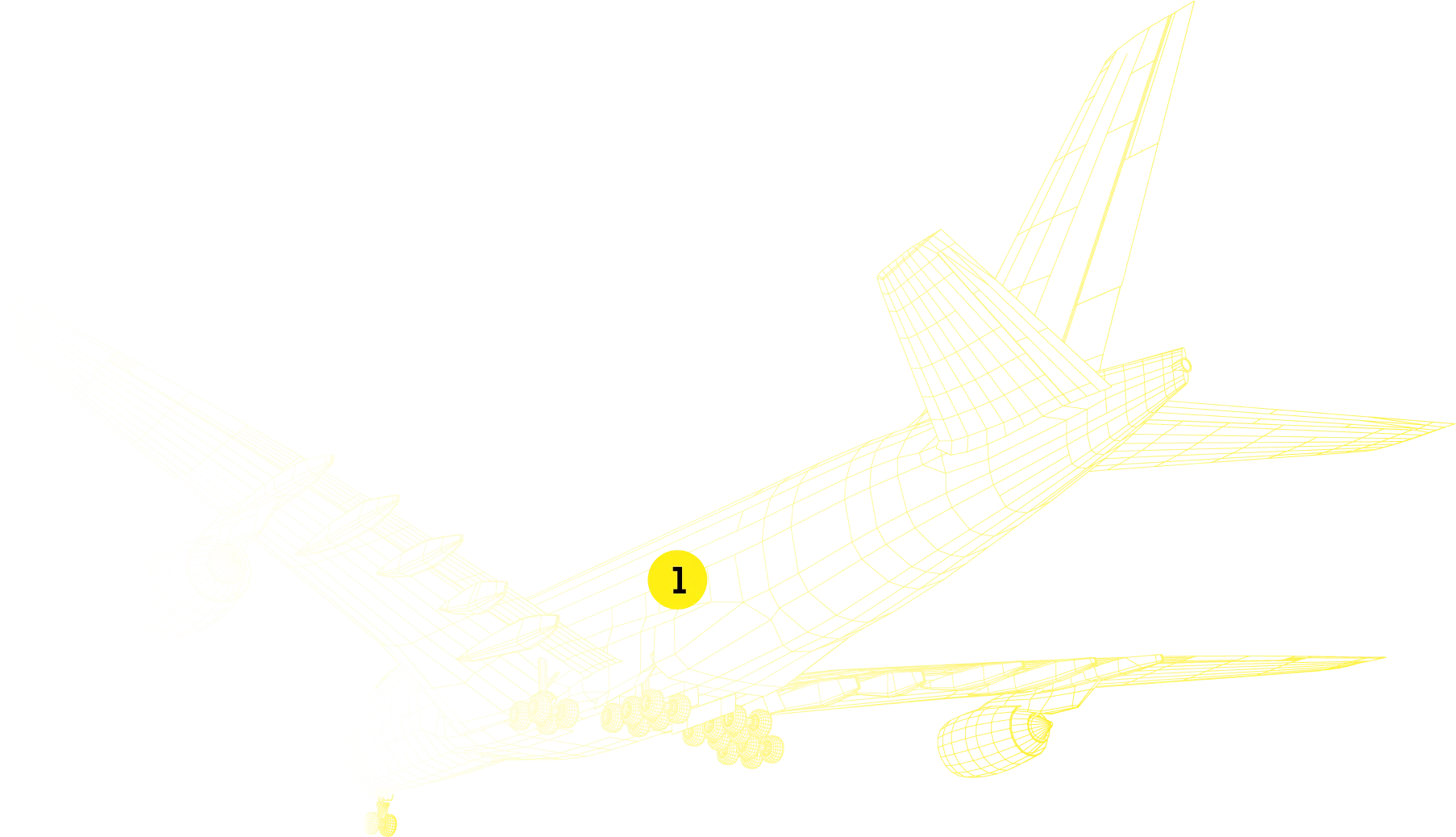
1. Plastic window covers
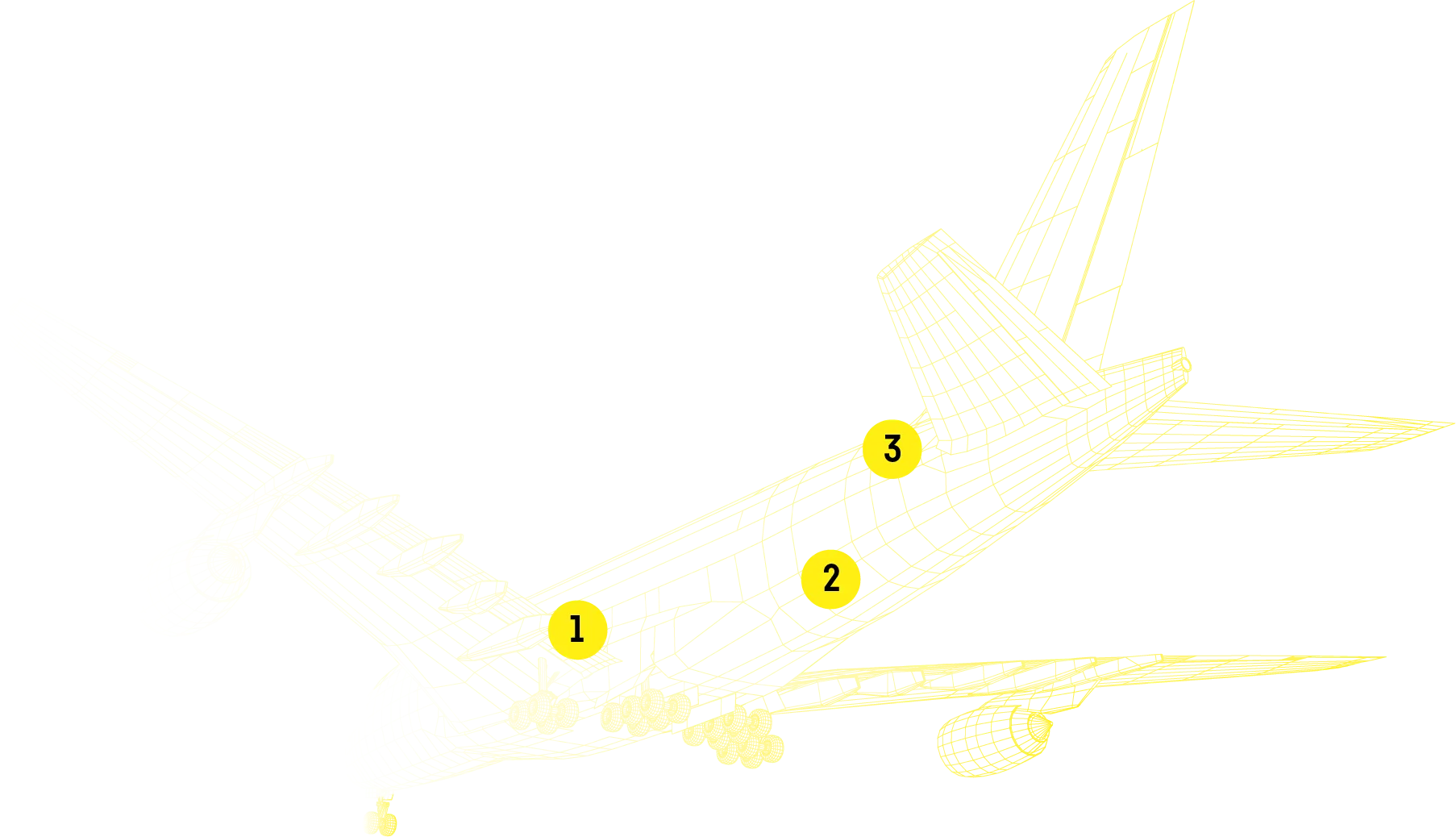
1. Galleys / kitchen
2. Interior floor panels
3. Overhead compartments
Railway application
Our technology is applicable to a wide variety of assembly parts.
Click on the parts to find out more.
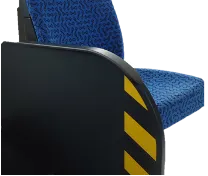
Seating and trim
Lorem ipsum dolor sit amet, consectetur adipiscing elit, sed do eiusmod tempor incididunt ut labore et dolore magna aliqua.
go to product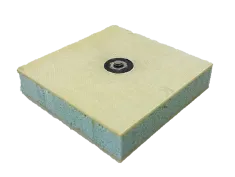
Floor trim panels
Sturdy fastening systems for floor trim panels in railway vehicles guarantee durability and stability, enhancing overall passenger experience.
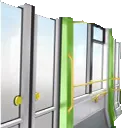
Side wall panels
Reliable fastening solutions ensure side wall panels in railway applications are securely attached, enhancing passenger safety and comfort.
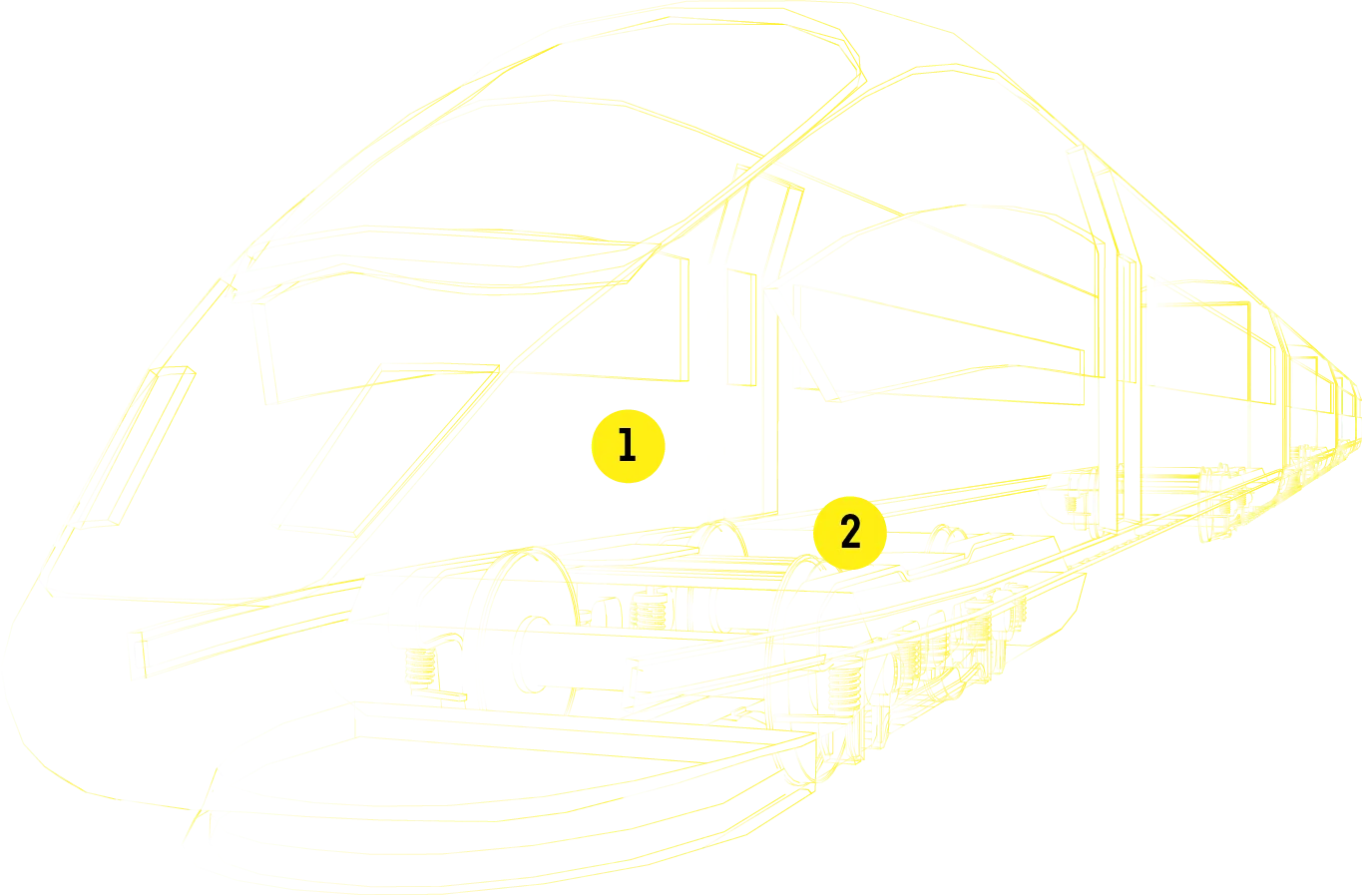
1. Seating and trim
2. Floor trim panels
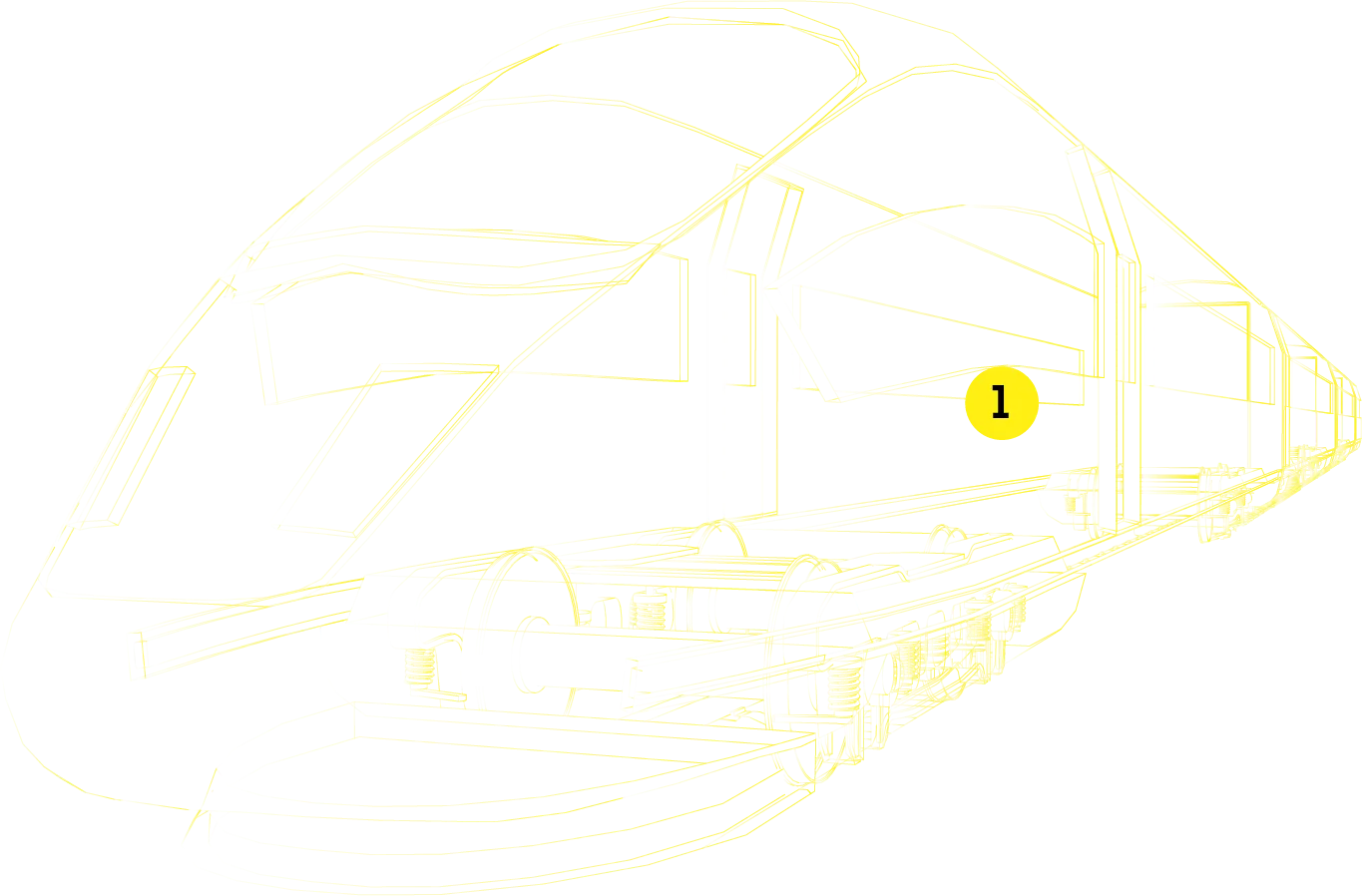
1. Side wall panels
HVAC application
Our technology is applicable to a wide variety of assembly parts.
Click on the parts to find out more.

Moisture control
Durable fastening systems effectively secure moisture control components, ensuring reliable performance in HVAC systems.
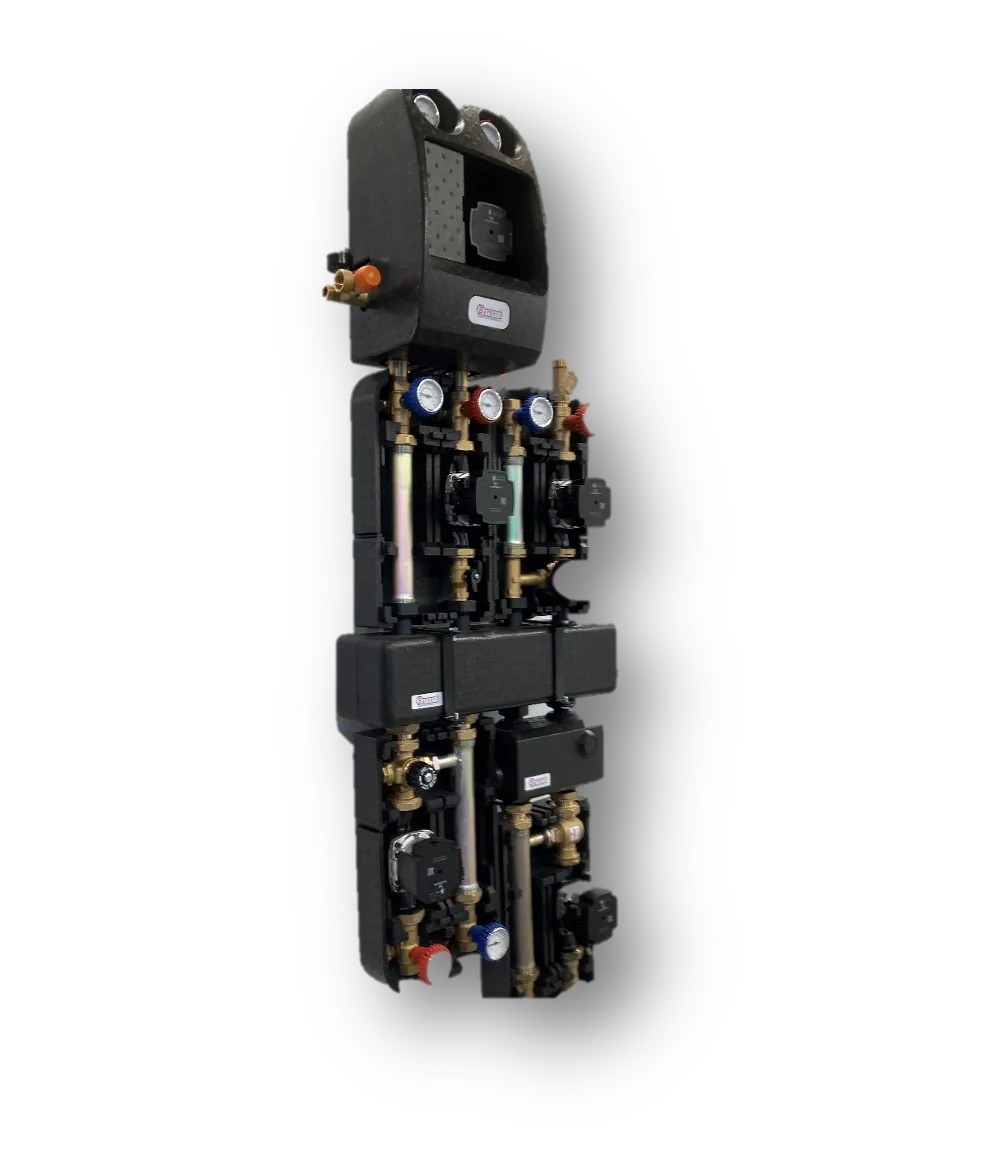
Control and operation units
Secure fastening techniques ensure control and operation units in HVAC systems are firmly mounted, guaranteeing stability and ease of use.
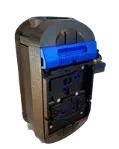
Air duct housing
Reliable fastening methods maintain the stability of air duct housings, ensuring efficient airflow management in HVAC systems.
1. Moisture control
2. Control and operation units
3. Heat pump enclosure
4. Air duct housing
Want to find out more about our technology?
Talk to our technical expert and ask away.
We’re looking forward to hearing from you.
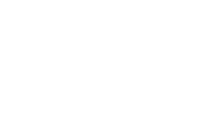