.00_01_53_06.Standbild001.webp)
AI powered quality assurance
In the dynamic world of ultrasonic welding, MM-Welding stands at the intersection of innovation and precision with our AI-powered SmartSolution. This groundbreaking system is a testament to our commitment to advancing manufacturing technology, offering an unparalleled level of quality assurance.
Embracing the principles of Industry 4.0, the SmartSolution harnesses the power of machine learning to elevate the efficiency, predictability, and reliability of welding processes. Dive into the realm where sophisticated AI meets the rigor of ultrasonic welding, and discover how our solution is transforming the landscape of manufacturing with unparalleled accuracy and control.
MM-Welding SmartSolution: Pioneering Quality assurance in various industries
Empowering Precision and Innovation Across Sectors
MM-Welding's SmartSolution is a revolutionary approach to ultrasonic welding, harnessing the power of AI and advanced data analytics. This innovative system transcends traditional welding methods, offering unparalleled precision, efficiency, and reliability for sectors including automotive, aerospace, and railway.
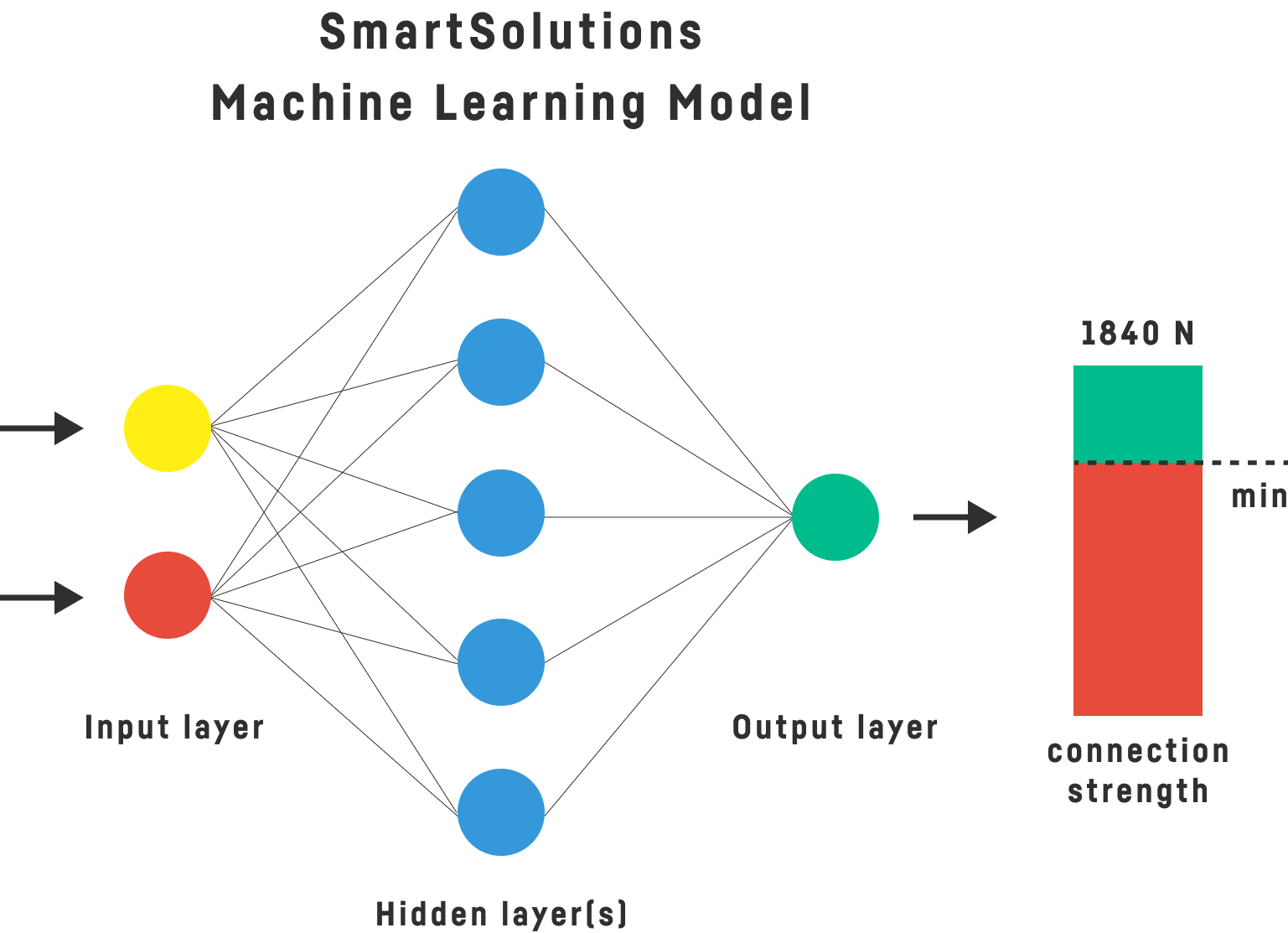
.00_01_53_06.Standbild001.webp)
Centralized Data Management for Enhanced Decision-Making
At the core of our SmartSolution is the SkillsBank (DataPool), a robust database that compiles essential welding data. This feature is critical in industries where data-driven decisions lead to superior product quality and operational efficiency. Coupled with automated data integration, it ensures that every phase of the welding process is monitored and optimized for the best results.
Precise Process Monitoring and Quality Control
Our advanced ultrasound technology is a cornerstone in achieving detailed process insights. This level of monitoring is crucial in industries where welding precision directly impacts product safety and performance. The integration of AI in our Smart Quality Control tool allows for real-time detection of irregularities, ensuring consistently high-quality welds. Additionally, the Performance Prediction tool, powered by machine learning, forecasts essential weld characteristics, further elevating the manufacturing process.
.00_01_14_10.Standbild015.webp)
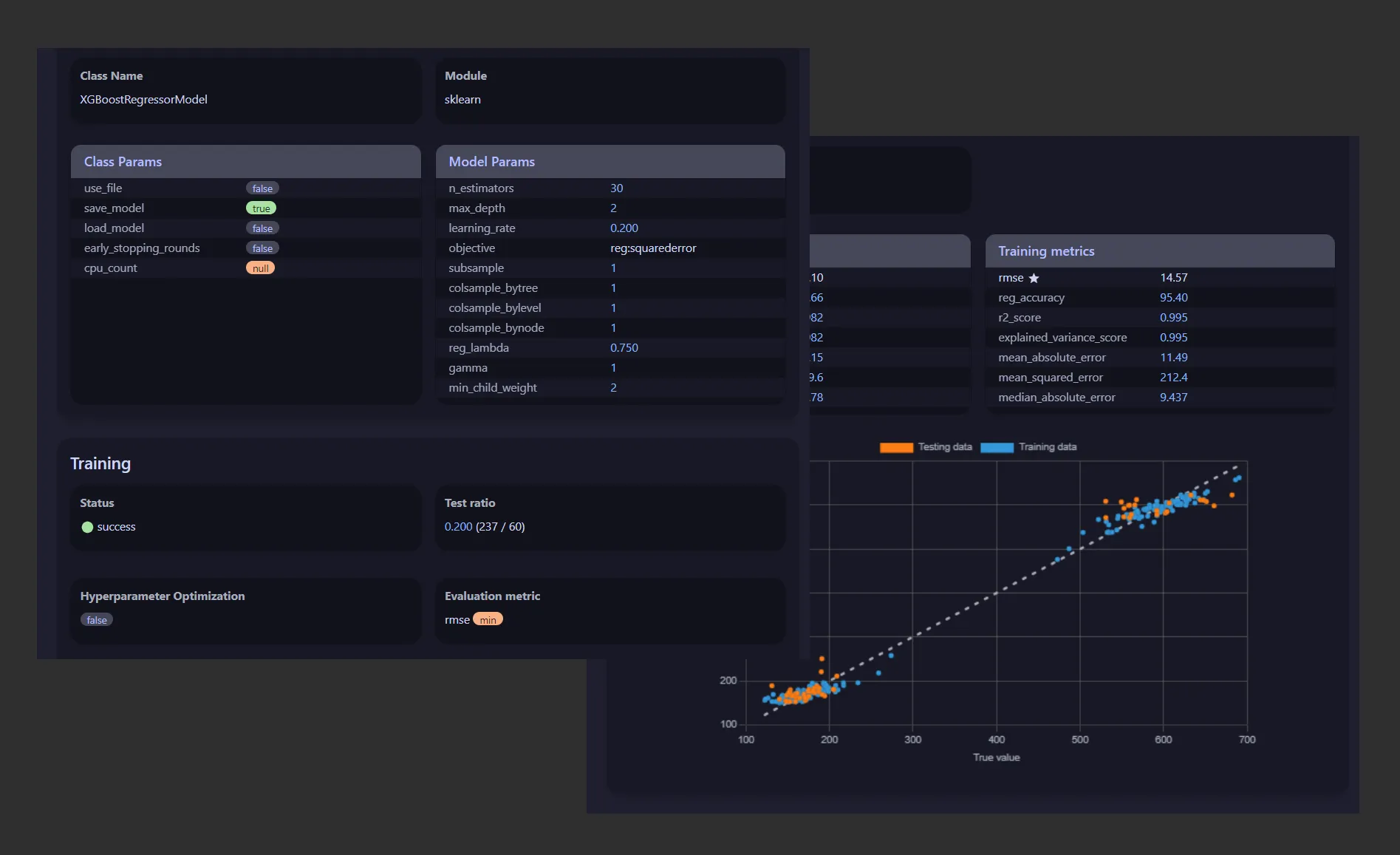
Leveraging Machine Learning for Predictive Analytics
Machine learning algorithms form the backbone of our predictive analytics, transforming vast amounts of manufacturing data into actionable insights. This capability is invaluable across various industries, enabling real-time adjustments and predictive maintenance to ensure optimal welding performance.
Seamless Hardware Integration and Robust R&D Support
The integration of our Hardware Box into existing production setups exemplifies our commitment to technological synergy, streamlining operations without disrupting existing workflows. Complementing this, our R&D simulation tools provide ongoing support for continuous process improvement and technological advancement.
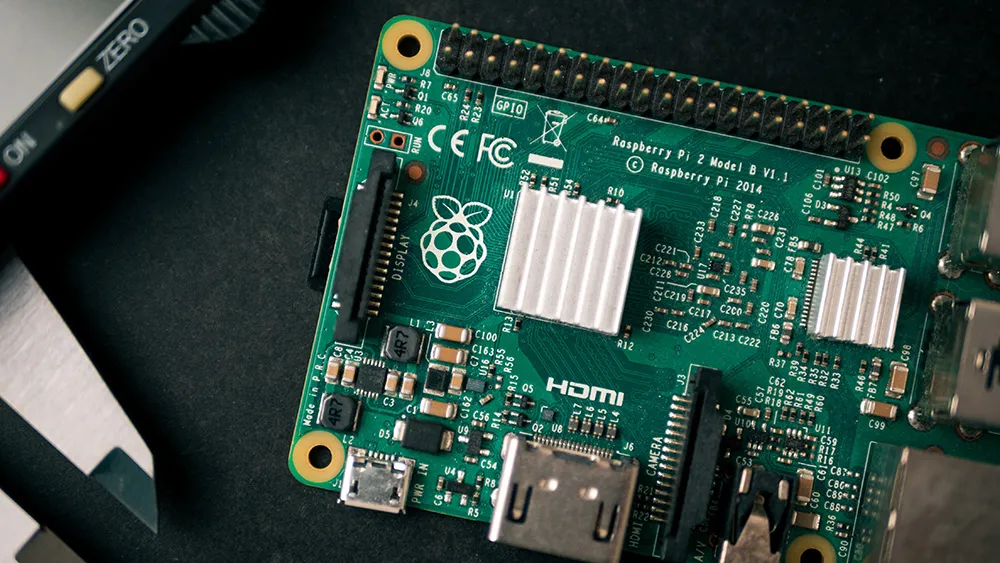
Want to find out more about our technology?
Talk to our technical expert and ask away.We’re looking forward to hearing from you.
TALK TO AN EXPERTOur solutions
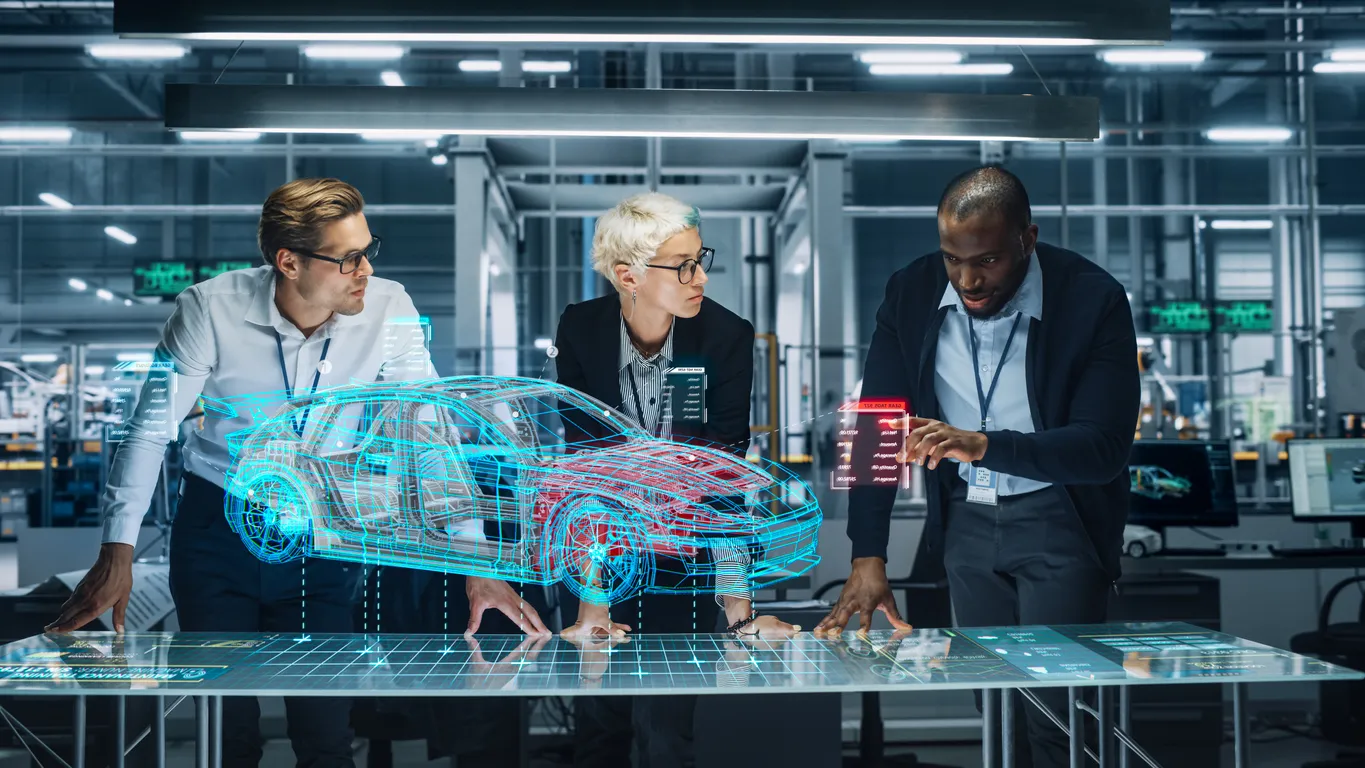
Engineering services
From customized product requirements resulting from customer challenges to rapid prototyping for real-world applications. Experience the power of advanced FEM tools to predict performance for optimized results. Rigorous testing, refinement and precision-guided production steps ensure excellent materials and aesthetic finesse.
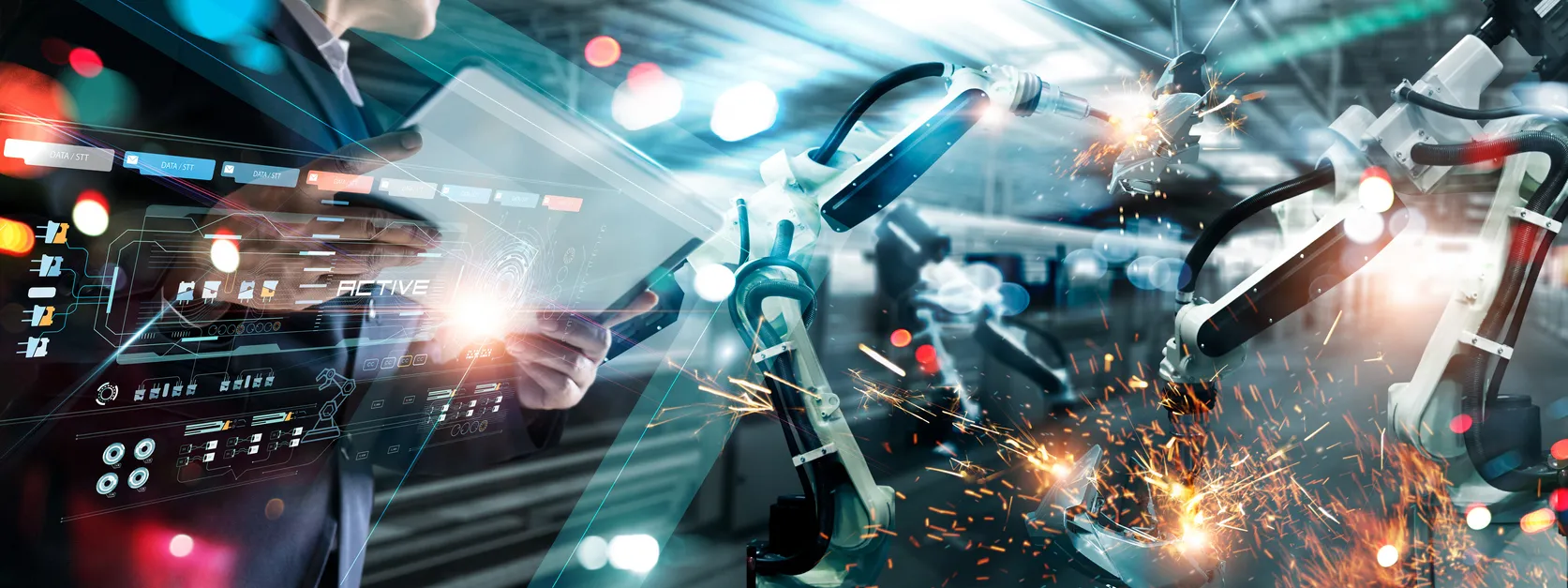
Assembly process
MultiMaterial-Welding AG's MM-Welding® technology is revolutionizing the manufacturing sector, particularly in automotive and aerospace industries. Our groundbreaking LiteWWeight® process embodies a new era of efficiency and precision in material joining. By moving beyond traditional methods, this technology offers a streamlined approach to assembly, enhancing productivity and output quality. It's a transformative solution, designed not just to replace but to significantly upgrade existing assembly processes.