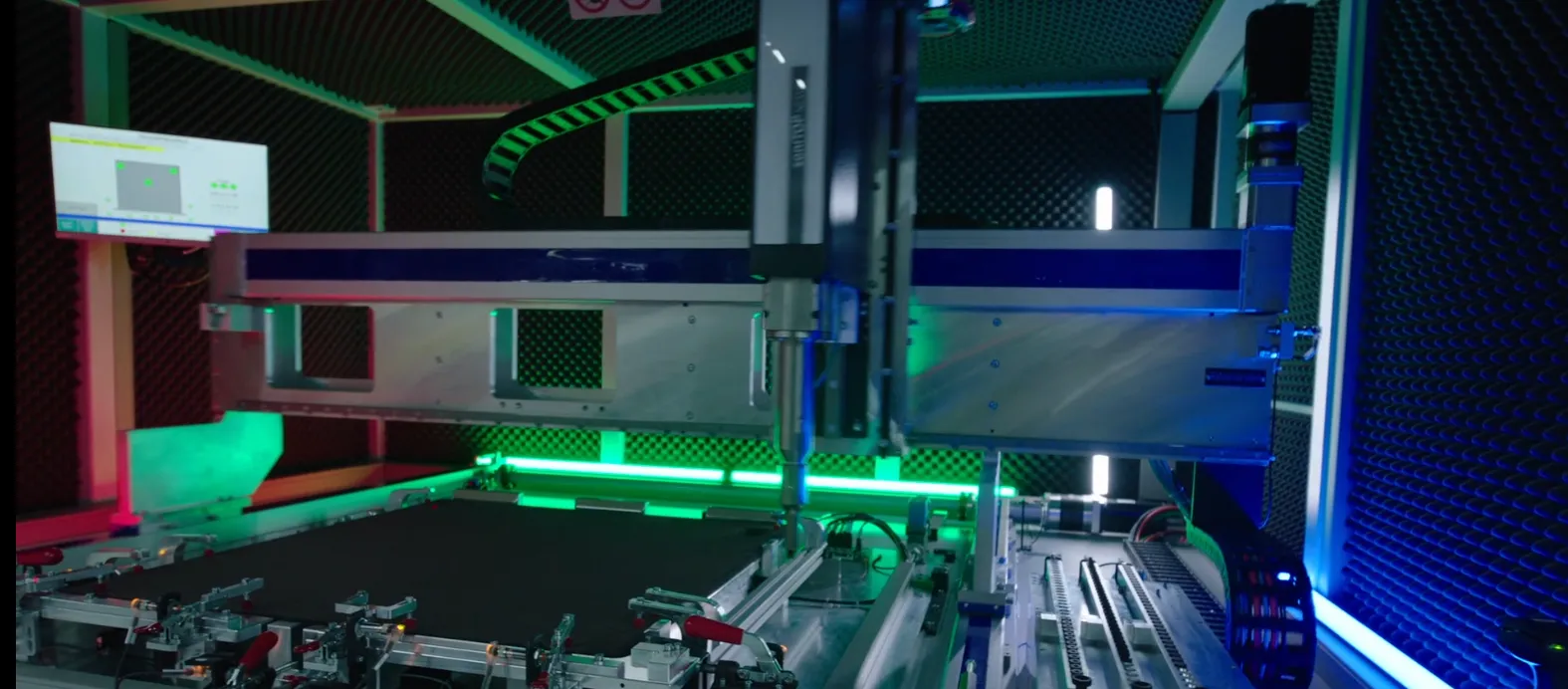
Optimizing the assembly process
MultiMaterial-Welding AG's MM-Welding® technology is revolutionizing the manufacturing sector, particularly in automotive and aerospace industries. Our groundbreaking LiteWWeight® process embodies a new era of efficiency and precision in material joining. By moving beyond traditional methods, this technology offers a streamlined approach to assembly, enhancing productivity and output quality. It's a transformative solution, designed not just to replace but to significantly upgrade existing assembly processes.
The integration of ultrasonic energy in our LiteWWeight® process marks a paradigm shift in material assembly. In the following sections, we delve into the core machinery and equipment that drive this innovative technology. We'll also explore its seamless integration into existing assembly lines, demonstrating how MM-Welding® can elevate your production capabilities to meet today's manufacturing demands for speed and precision.
We provide you the full process offer including the production machines.
Table top machines
With the basic table top machine the part is handled totally manual by the worker. You can choose having the ultrasonic unit on a small or big table, a table on wheels, a scissor table or any table design you like. The possibilities on nest building and part handling are endless, depending on your needs. The welding process always has to be started manually by a hand button or foot switch. Machine parts can easily and quickly be changed, so that you are able to weld various products one after the other.
X-Y-Portal machines
With the X-Y-Portal machine you can easily run smaller cycles or serial productions. Nesting and programming can be changed whenever needed. By adding feeding systems, clamps and noise housing you can build your prefect machine to get the maximum out of your flexible production. With different programming options the machine can weld many welding points in one sequence while the worker has time to prepare the next part.
Dedicated machines
The dedicated machines are perfectly adapted and dedicated to your needs and products. The perfectly tailored nesting, different feeding systems, the number of parts processed per cycle time, noise isolation options, turntable solutions - there are no limits to your customized machine to get the best out of your production. Even welding points in different heights or angles or welding from the bottom side – there are no limts.
Robotic machines
Integrating MM-Welding® technology into existing assembly lines is a straightforward and highly beneficial process. The modular nature of the ultrasonic welding unit allows for easy adaptation to different production environments, accommodating various material types and thicknesses without requiring significant line alterations. The equipment’s compact footprint and user-friendly interface ensure it can be seamlessly incorporated into existing workflows, enhancing efficiency without disrupting established processes.
The Smart Robotic MM-Welding® system is particularly conducive to integration. Its robotic automation capability is designed to be flexible, adapting to various operational layouts and production demands. This adaptability allows for the automation of complex tasks, reducing manual labor and increasing throughput. The system's machine learning component provides real-time process optimization, ensuring consistently high-quality outputs and adapting to diverse manufacturing needs. Moreover, the equipment's longevity and low maintenance requirements make it a cost-effective solution, promising long-term operational efficiency and reliability. By integrating MM-Welding® technology, manufacturers can significantly upgrade their production capabilities, paving the way for increased productivity, reduced waste, and enhanced product quality.
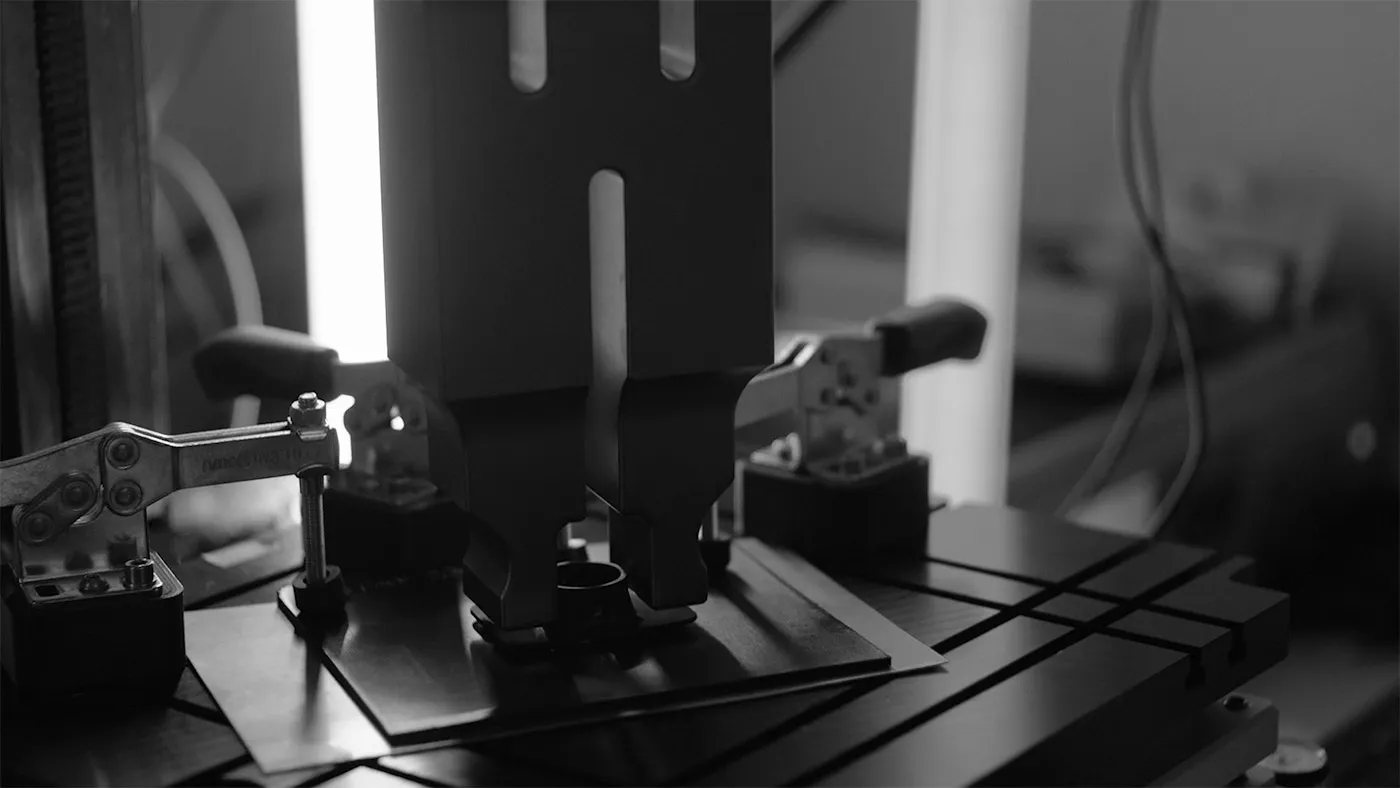
Simplifying assembly:
a leap towards efficiency
Streamlining complex processes
LiteWWeight™ technology condenses multiple traditional steps into a singular, fluid motion. This integration not only simplifies the assembly process but also drastically reduces the time and effort involved.
Automating for consistency
By automating critical steps, LiteWWeight™ minimizes human intervention, leading to consistent quality and repeatability in every assembly cycle.
Optimizing production flow
With its rapid execution and precision, the technology enhances the overall production flow, allowing for more units to be assembled in less time, without sacrificing quality.
Reduced wear and tear on equipment
The LiteWWeight™ technology's ultrasonic approach significantly lessens the physical strain on assembly equipment. Traditional methods, which often involve more rigorous mechanical processes, can lead to quicker wear and tear. By employing ultrasonic energy for connections, the physical impact on machinery is minimized, leading to longer equipment lifespans and reduced maintenance costs. This not only streamlines the assembly process but also translates into long-term cost savings and increased equipment reliability.
Want to collaborate with us?
Find out from our technical expert how our customers save time and money with our solutions.
TALK TO AN EXPERTDiscover past projects
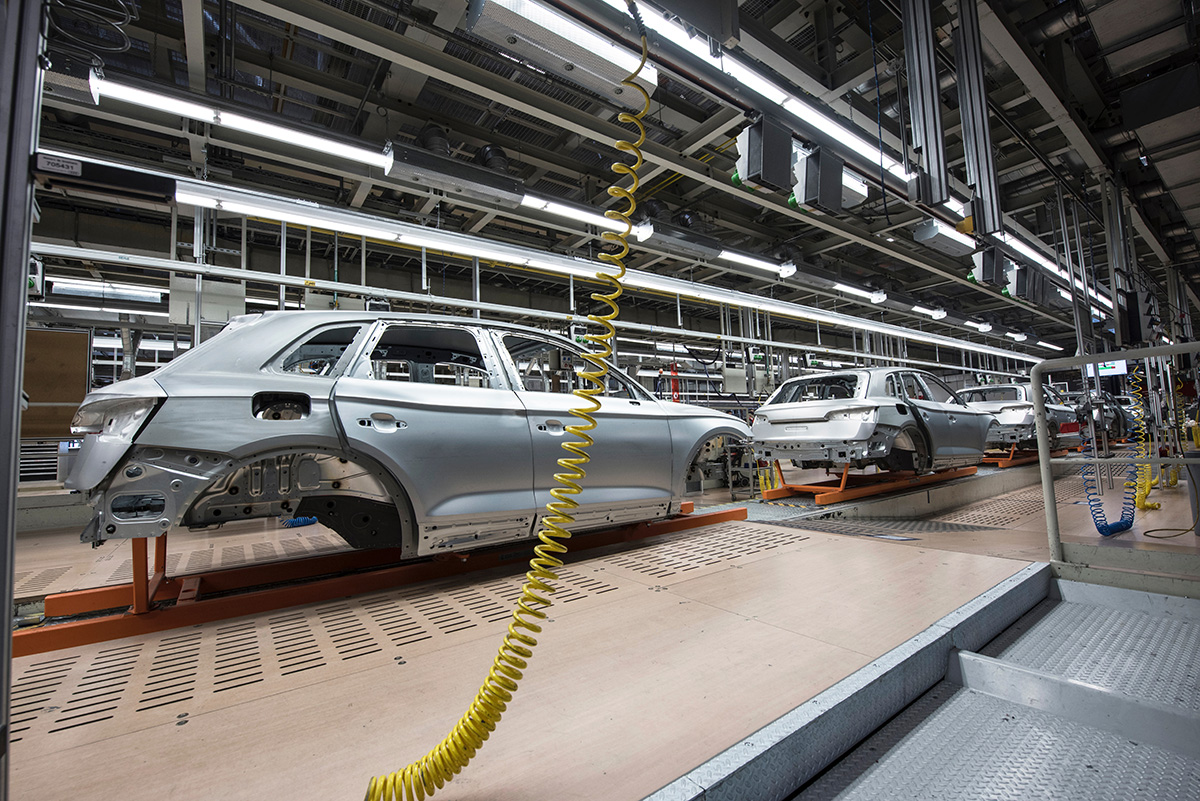
Revolutionizing Automotive Safety with Storopack
Uncover the groundbreaking collaboration between Storopack and MultiMaterial-Welding in developing a unique crashpad solution for premium automobiles, marking a significant advancement in automotive safety technology.
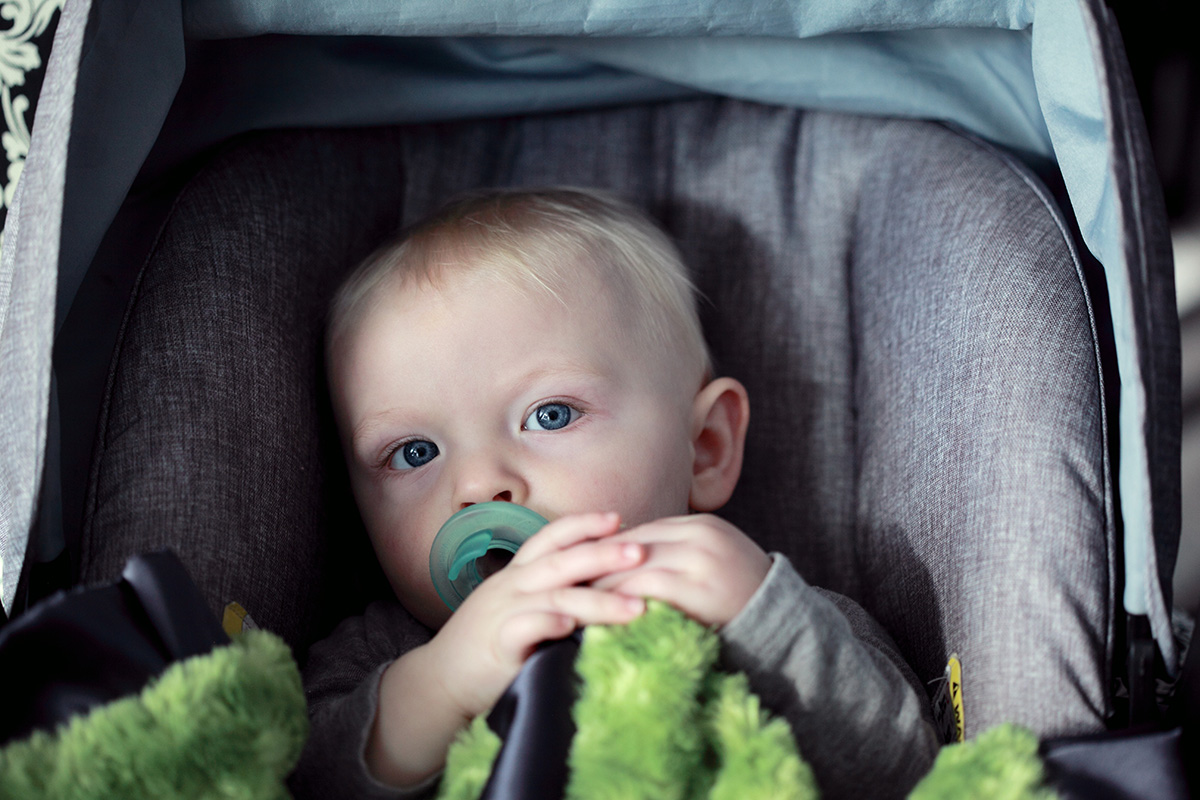
Innovative Fastening Solutions for Child Safety with SWANDOO
Discover how SWANDOO, a leader in child seat innovation, leveraged our MM-Welding® technology to create the "Marie" series, blending safety, design, and resilience in child transportation solutions.